Everything you need to know about Expanded Polystyrene (EPS)
Expanded Polystyrene (EPS) is one of the most widely used foams in the packaging and construction industry and yet one of the least recycled types of plastic resulting in significant amounts of environmental damage.
How Expanded Polystyrene is made
The process of creating polystyrene begins with the production of styrene, a petrochemical and the base monomer. The majority of Styrene, around 80 per cent, is produced by the dehydrogenation of ethylbenzene, which in turn is made by a reaction between benzene and ethylene using a catalyst of aluminium chloride. In more modern operations, this has been replaced by zeolites.
When styrene molecules are linked together into a polymer, polystyrene is formed. Polystyrene is an inert plastic which can be used to make a wide range of products, the most common of which is polystyrene foam or Expanded Polystyrene also commonly referred to as Styrofoam.
Styrofoam was created by a scientist at Dow Chemical Co in the 1940s trying to make a new rubber by combining styrene and isobutylene but accidentally came upon Styrofoam which is much lighter and more flexible than polystyrene.
Expanded Polystyrene is made from solid beads of polystyrene that contain an expansion gas, today most commonly pentane, that is dissolved into the bead at the time of manufacture.
When these solid polystyrene beads are exposed to heat in the form of steam, the pentane in them expands causing the solid bead to expand to about 40 times its original size, these are known as pre-puff or expanded beads. To you and me they are known as beanbag filling.
These expanded polystyrene beads can be further processed by being loaded into moulds and steamed again to create blocks of various sizes, shapes and densities. These can be cut into sheets or blocks of varying thicknesses.
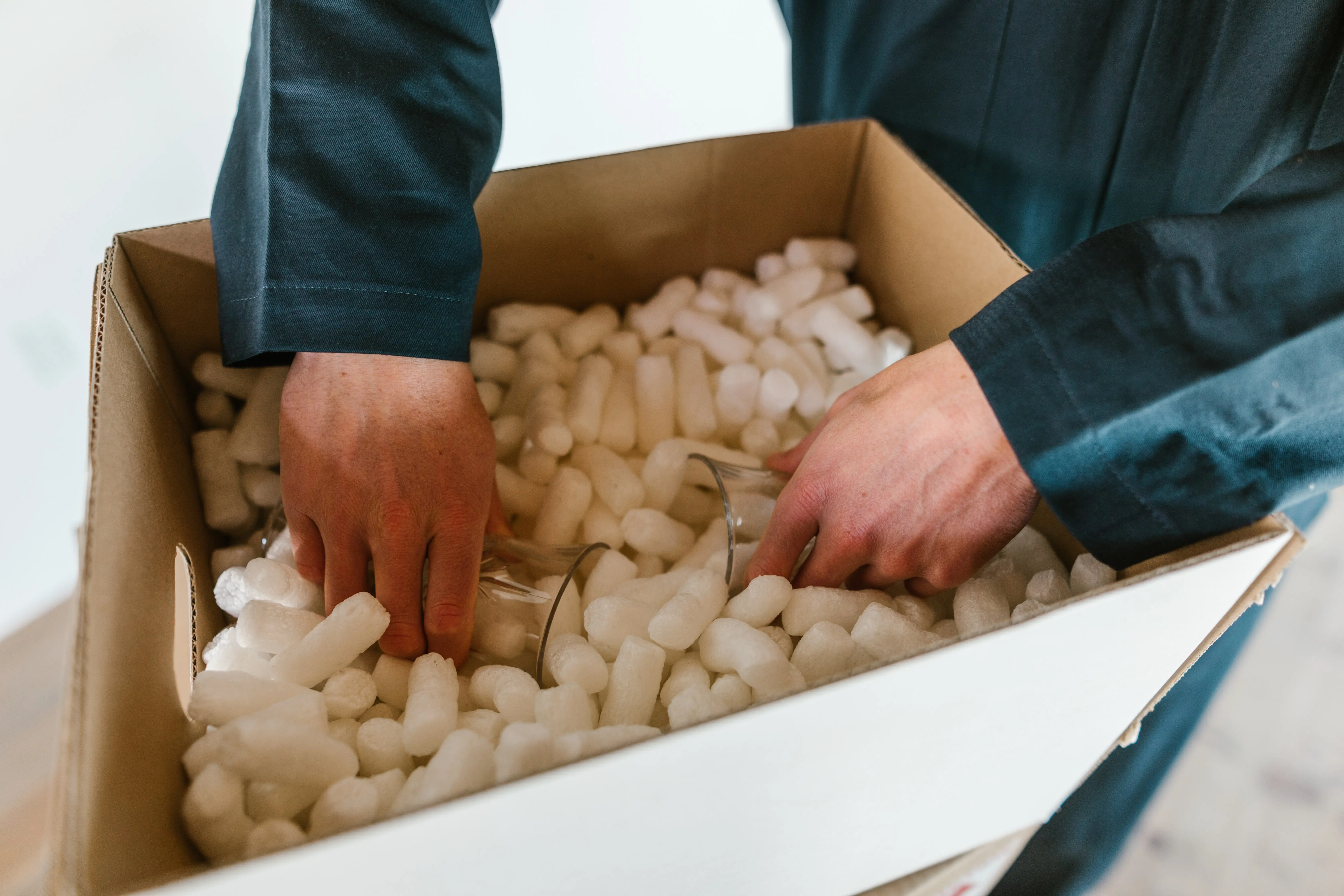
Uses of Expanded Polystyrene
Styrofoam like polystyrene has a vast number of applications and is used to make consumer products such as disposable plates, cups and other food service-related containers.
Styrofoam and EPS are also used heavily in the construction industry. Expanded Polystyrene insulation is lightweight, rigid and has a closed-cell structure which allows for minimal water absorption and low vapour permanence. It can be made to various compressive strengths to withstand different loads and backfill forces. It is also much more cost-effective than other types of insulation materials.
Due to these characteristics and customisability, it is now globally recognised as a solution for thermal insulation making it an ideal choice for green building design by offering practical environmental advantages that can maximise energy efficiency and reduce operational costs in the long run while also providing improved indoor environmental quality and enhancing structural durability of the building itself.
The packaging industry is another large consumer of Styrofoam or EPS mainly in the electronics segment and especially for fragile electronic goods such as TVs and laptops. Styrofoam helps keep the products in place when in their cartons and also acts as a shock absorber protecting the goods from damage, particularly during transport. This industry also uses Expanded Polystyrene in the form of puff beads or alternatively what is known as packaging peanuts to ship smaller fragile items that do not come with Styrofoam protection in their cases.
Some of the more modern uses that have been found for Expanded Polystyrene is for the transport of Covid 19 vaccines thanks to its insulating properties. EPS fish boxes have been used for a while for the same reason. These are a convenient solution for the protection of fish and other seafood products from seaport to sales counter due to their unrivalled combination of thermal performance, impact protection and stacking strength.
Super-insulating EPS beehives are another new use Styrofoam has found. It helps keep bees warmer in the winter and cooler in the summer so they require less food to survive, spend less time searching for food and therefore have more time to make honey. EPS beehives of high density are also highly resistant to moisture, this in turn prevents the spread of mould that is common with wooden beehives, so they can last many years more.
Positive Environmental Impacts of Expanded Polystyrene
EPS or Styrofoam has a low carbon impact thanks to a relatively clean, low-pollution manufacturing process using technology that results in minimal energy and water inputs with barely any production waste. As steam is the key heating ingredient and the water is re-used many times, there is no waste generated. Even the rejected pieces get reused in the system.
Most modern manufacturing plants have a pentane collection system for air quality control. This system captures the pentane that is released during production and reroutes it to the boiler. This helps reduce the amount of fuel used saving resources while being environmentally responsible.
Expanded Polystyrene does not contain environmentally damaging chlorofluorocarbons (CFCs) or hydrochlorofluorocarbons (HCFCs) when pentane is used as the blowing agent. Pentane has a low Global Warming Potential (GWP) of less than five which means that the European Union does not register pentane as a substance that is hazardous to human health or the environment.
Due to its high structural strength and extremely low weight Expanded Polystyrene when used in place of wooden containers greatly reduces the overall weight of the cargo and therefore uses less fuel in transport.
The protective performance of Expanded Polystyrene also helps to reduce wastage in various supply chains. Due to its cell structure, the use of EPS helps prevent food wastage as it protects the food for longer compared to conventional crates and avoids damage in the different stages of production and shipment from farm to fork, ensuring many different foods reach the retailer and consumer in perfect condition minimising rejects.
The protection offered by EPS also helps to reduce wastage caused by goods that would otherwise be broken or damaged in the supply chain and sent back to be disposed of.
Negative Environmental Impacts of Expanded Polystyrene
Expanded Polystyrene packaging keeps our food to go hot, insulates our buildings and helps safely transport everything from fresh fish to TVs, and even human organs, all around the world.
Although the achievements are amazing, the havoc it wrecks on our natural environment is far from amazing. We see it nearly every day, everywhere, often blown onto roads after tumbling out of bins or being disposed of carelessly.
Expanded Polystyrene is a kind of plastic made from chemicals that come from oil and gas. Styrene is one of the main ingredients in EPS and has been found to be a known carcinogen, although research shows that unless the exposure is extremely high, styrene does not cause any adverse health effects.
Expanded Polystyrene like other plastics is generally non-biodegradable and often seen as a negative factor environmentally. When disposed of improperly or leaks out of the supply chain, it can harm wildlife and last for years and years. Another concern is the number of compounds and chemicals which are incorporated during production that can enter the environment either by leaching or through degradation of the material.
Surveys conducted by the Marine Conservation Society indicate that it is a consistent component of litter on the coasts with an average of 182.6 pieces of plastic or expanded polystyrene turning up on every 100m of beach surveyed. A lot of this ends up in the sea eaten by fish which we can end up consuming ourselves.
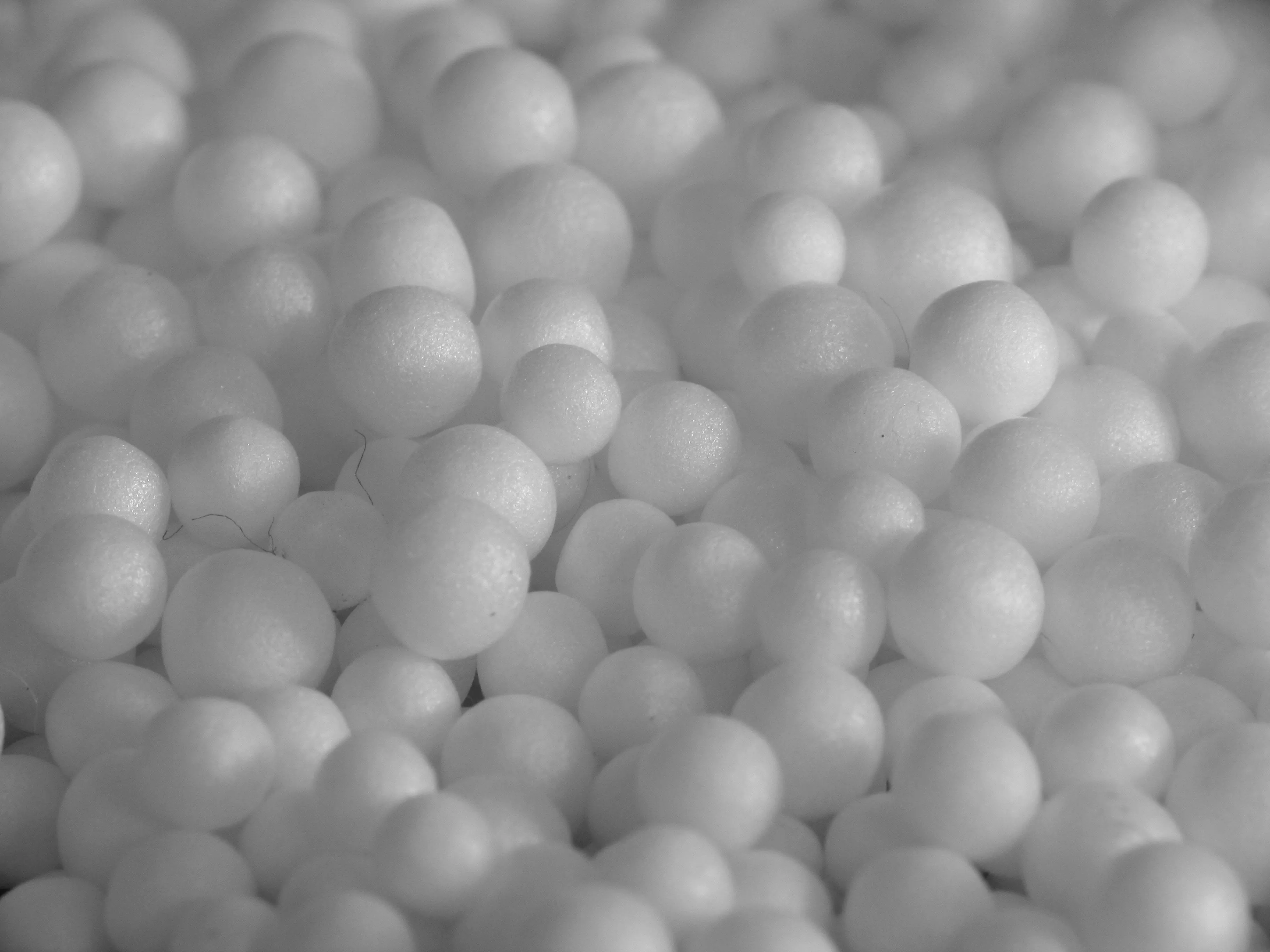
How to Dispose of Expanded Polystyrene
Expanded Polystyrene foam is slow to degrade but on the other hand it is 100 percent recyclable. Sadly, however, out of the roughly 16 million metric tons of EPS produced every year a little less than 1 percent of it is recycled.
Recycling is the smartest way to keep Expanded Polystyrene out of our environment. EPS can be efficiently recovered and recycled especially when done at source. EPS that comes from packaging waste for example is an ideal source for recovery schemes.
In order to be recycled the Expanded Polystyrene must first be cleaned before further mechanical or solvent treatment. This will return it back to a raw material again which can then be used to make new products keeping it completely out of the environment.
Recycling must be done at specialised facilities as not all plastic recyclers accept Expanded Polystyrene and Styrofoam. Look for expanded polystyrene (EPS) or styrofoam recycling drop-off centres closest to your area.
If you are in the Middle East, Green Theory’s waste management and styrofoam recycling solutions could help you with your EPS recycling needs. Contact our team today.